Nachrichten
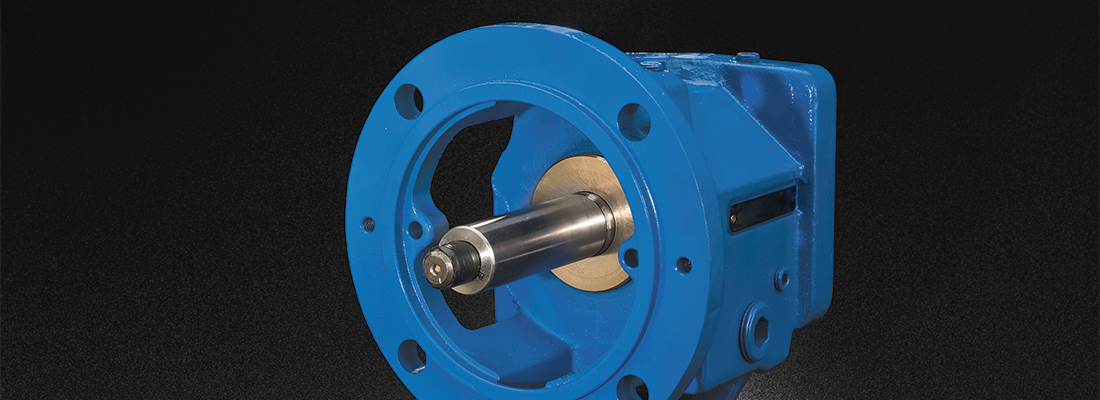
Sechs Gründe für Schmiermittellecks in Bearing Isolators (Lagerschutzdichtungen)
Achten Sie auf diese häufigen Fallstricke und gehen Sie nicht davon aus, dass ein Schmierstoffleck ein Dichtungsversagen bedeutet.
Schmieröl, das aus dem Lagergehäuse austritt, wird häufig als Versagen der Lagergehäusedichtung interpretiert. Für die meisten Betreiber ist die Analyse einfach: kein auslaufendes Öl bedeutet, dass die Dichtung in Ordnung ist, während auslaufendes Öl einem Dichtungsversagen gleichkommt. Dies gilt zwar für Kontaktdichtungen, doch Lecköl aus einem Bearing Isolator ist höchstwahrscheinlich auf andere Faktoren als das Versagen der Dichtung zurückzuführen.
Nachstehend einige der häufigeren Ursachen für Bearing Isolator-Schmiermittelleckagen in Prozesspumpen
1. Zu viel Öl
Es scheint einfach, doch die häufigste Ursache für die Leckage eines Bearing Isolator an Prozesspumpen ist ein überfülltes Lagergehäuse. Es ist inzwischen gängige Praxis, das Wartungsfachleute bis zur maximalen Füllgrenze, wenn nicht sogar etwas darüber, füllen. Dabei wird davon ausgegangen, dass im Falle einer Leckage zusätzliches Schmiermittel zur Verfügung steht. Doch diese Praxis kann unbeabsichtigt zu Leckagen beitragen. Glücklicherweise wird die Leckage bei Bearing Isolators gestoppt und sie funktionieren wieder normal, wenn der Ölstand auf das richtige Niveau zurückgebracht wird Es kann zu etwas Ölleckage kommen, wenn sich die Dichtung von überschüssigem Schmiermittel reinigt, doch das sollte mit der Zeit abnehmen.
2. Ausrichtung
Die meisten Bearing Isolators verfügen über eine Schmiermittelrückführung, die in ihre jeweilige Labyrinthstruktur integriert ist. Die Rückführung muss in der unteren Totpunkt- oder Sechs-Uhr-Position des Bearing Isolators installiert werden, um einwandfrei zu funktionieren. Dadurch kann das Öl leicht in den Lagersumpf zurückfließen. Eine der häufigsten Ursachen für eine falsche Dichtungsausrichtung ist mangelnde Schulung oder unklare Installationsanweisungen.
3. Versperrter Schmiermittel-Rücklaufweg
Die meisten modernen Bearing Isolators sammeln Spritzschmiermittel in ihren jeweiligen Labyrinthstrukturen. Sobald das Schmiermittel gesammelt ist, muss es über einen klaren, ungehinderten Weg in den Lagersumpf zurückführbar sein.
Der Rücklaufweg zum Lagersumpf kann durch Gegenbohrungen im Gehäuse blockiert sein, die ursprünglich als positiver Anschlag für eingepresste Lippendichtungen vorgesehen waren. Im Bereich zwischen dem Lager und der Lagergehäusedichtung kann ein Abflusskanal fehlen. In einem solchen Fall sammelt sich in diesem Bereich Schmiermittel an, bis der Bereich vollständig geflutet ist und die Dichtung undicht wird.
Um dieses Problem zu beheben, muss der Bereich zwischen dem Lager und dem Bearing Isolator einen ungehinderten Rücklaufweg zum Lagersumpf aufweisen. Wenn das Schmiermittel nur durch das Lager in den Lagersumpf abfließen soll, führt dies wahrscheinlich zu einer Schmiermittelleckage.
4. Unsachgemäß eingesetzte Außenöler
Außenöler sind äußerst positionsempfindlich und müssen auf der richtigen Seite des Gehäuses in Relation zur Drehrichtung der Welle gemäß den Richtlinien des Herstellers installiert werden. Öler müssen gerade und vierkant eingebaut werden. Darüber hinaus muss die Leitung, die den Außenöler mit dem Lagergehäuse verbindet, ausreichend gefurcht sein, um Vibrationen oder Rütteln des Ölers zu vermeiden. Fragwürdige Installation können zu einer Überfüllung des Lagergehäuses und anschließendem Schmiermittelaustritt führen.
5. Wind
Heftiger Luftstrom über einem Lagergehäuse kann Schmiermittelleckagen verursachen, indem er eine Druckdifferenz zwischen der Innen- und Außenseite des Lagergehäuses erzeugt. Kupplungen und externe Kühlgebläse, die an den Lagergehäusen der Pumpen angebracht sind, sind eine potenzielle Quelle für schädliche Luftströme. Spaltfreie, solide Kupplungsschutzabdeckungen, die die Lagergehäusedichtungen mit wenig oder keinem Spalt um das Lagergehäuse herum umschließen, können Leckage verursachen.
Wenn ein Teil der Kupplungs- und Gebläseschutzabdeckungen nicht durch feste Oberflächen, sondern durch dichte Gitter erreicht wird, ermöglicht dies bei Einhaltung aller erforderlichen Sicherheitsvorkehrungen einen besseren Luftstrom und trägt dazu bei, den Druckaufbau zu verhindern.
6. Unsachgemäße Auswahl berührungsloser Dichtungen
Einige Bearing Isolators sind speziell für Fettschmierung und andere für Öl- oder Ölnebelschmierung ausgelegt. Einige Ausführungen können alle Schmierungsarten in einer einzigen Ausführung aufnehmen. In einigen Fällen können Vorteile erzielt werden, indem Bearing Isolators für bestimmte Anwendungen konstruiert werden, anstatt Standardkatalogartikel heranzuziehen. Beispielsweise kann bei Pumpenlagergehäusen mit einem hohen Anteil an Schmierstoffspritzern die Labyrinthstruktur so ausgeführt werden, dass sie direkt mit dem Schmiermittelrücklaufweg kommuniziert, was die Effektivität erheblich steigern.
Erfahrene Anbieter von Bearing Isolators können kundenspezifische Dichtungen schnell und wirtschaftlich konstruieren und sicherstellen, dass die Dichtungsausführung alle Bedenken berücksichtigt und für bestmögliche Zuverlässigkeit angewendet wird. Die Zeit, die für technische Aufgaben im Vorfeld aufgewendet wird, zahlt sich aus und stellt sicher, dass die Bearing Isolators wie vorgesehen funktionieren.
Verschleißfreie Bearing Isolators haben den Vorteil, dass sie nach ordnungsgemäßer Anwendung jahrelang im Wesentlichen störungsfrei, ohne Leistungsverlust arbeiten. Die Herausforderung liegt darin, dass sie etwas mehr Aufwand für Anwendungsdetails erfordern. Der Zeitaufwand für die Überprüfung einiger einfacher Parameter kann viel dazu beitragen, einen störungsfreien Betrieb zu gewährleisten.