Reduce Costs in Wind Turbines
Wind power has emerged as a leading technology for clean, sustainable energy. Even with this success, the industry suffers from high maintenance costs. Many of these costs are caused by bearing failure and lubrication issues due to ineffective sealing solutions.
Inpro/Seal, the inventor of the Bearing Isolator, offers proven sealing solutions to improve equipment reliability in wind turbines, significantly reducing maintenance costs.
Improve Equipment Maintenance Today
Inpro/Seal has been providing permanent bearing protection to rotating equipment for over 40 years. Learn how we can increase wind turbine reliability with proven solutions.
Fill out the short form to have an Inpro/Seal representative contact you shortly.
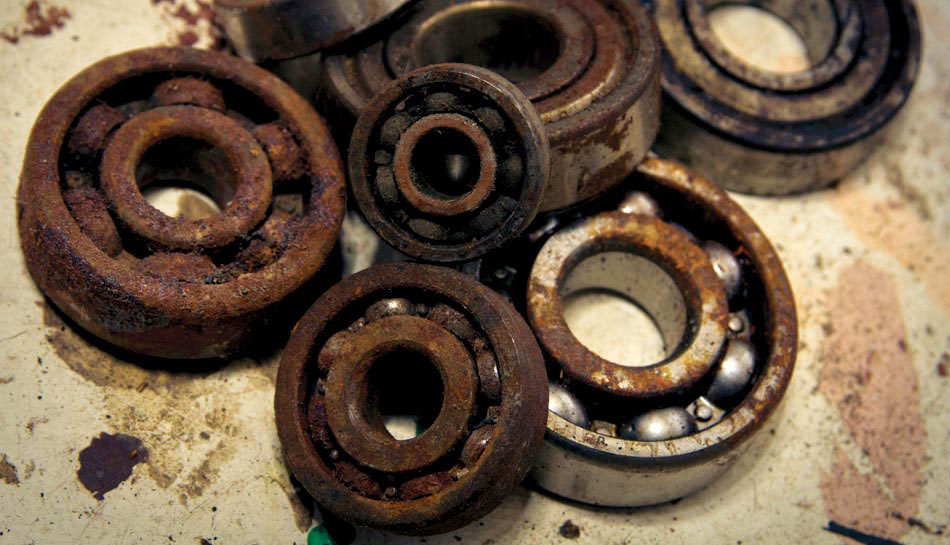
The High Cost of Bearing Failure
Wind turbine nacelles house the power transmission components of the wind turbine, including the gearbox and generator. These expensive and critical systems still rely on ineffective contact sealing methods to protect the bearings. Contact seals are low cost options that lead to high cost issues. Because of their contacting nature, they are prone to leakage, can damage or groove the shaft and have a finite life. When they fail, contaminants enter the bearing housing and lubrication escapes, putting these crucial systems at risk of failure.
Lost Revenue from Power Loss
Contact seals rely on consistent contact between the shaft and seal to function properly. At the point of contact, friction and heat are generated, requiring additional power to overcome the drag on the shaft. The additional power used to overcome a contact seal is power that can’t be sold to the grid. The more contact seals in the power train, the more power lost. Spread across a wind farm on an annual basis, the power loss and lost revenue can be significant.
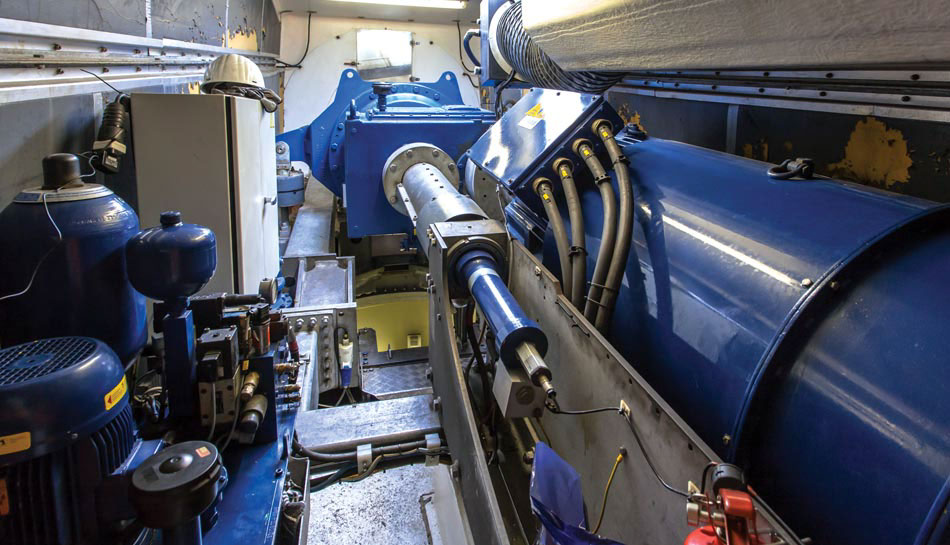
Decrease Bearing Failure & Power Loss With Non-Contacting Bearing Protection That Works
Introducing the Inpro/Seal Bearing Isolator
Inpro/Seal invented the Bearing Isolator in 1977 and has been providing permanent bearing protection to rotating equipment for over 40 years.
The Inpro/Seal Bearing Isolator permanently protects against contamination ingress and lubrication loss, extending bearing life and significantly reducing high repair or replacement costs on wind turbine equipment. A non-contacting compound labyrinth seal that is fixed to the housing, the Inpro/Seal Bearing Isolator is maintenance free with no wearing parts, designed to last the lifetime of your equipment.
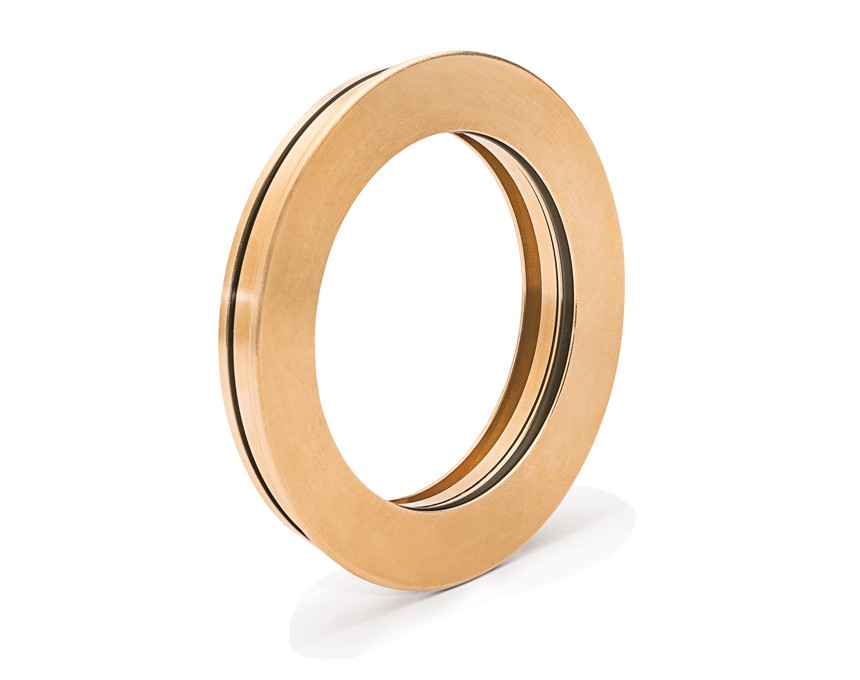
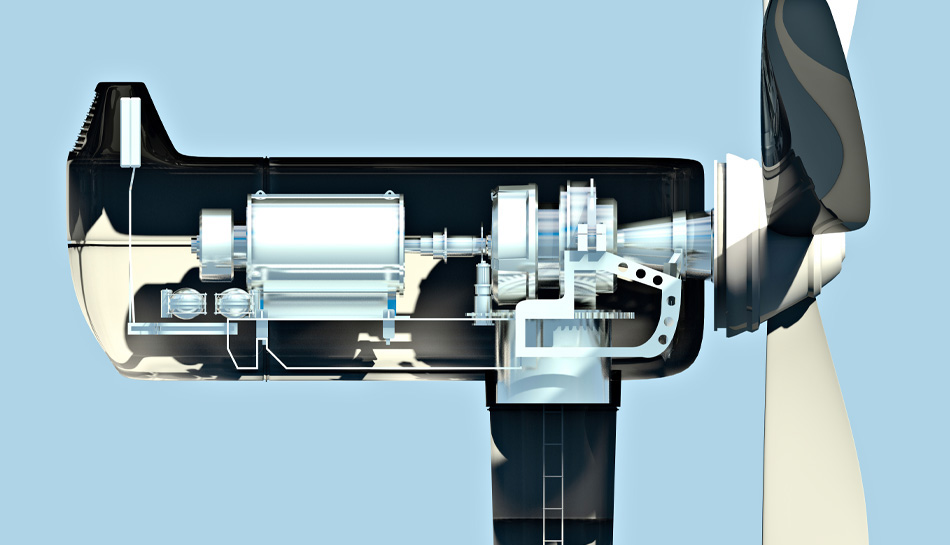
Case Study
Inpro/Seal Bearing Isolator Increases Wind Turbine Reliability
A wind turbine generator was suffering from grease leakage and power loss due to lip seal failure. Learn how Inpro/Seal Bearing Isolators solved the issue and saved the day.
Learn More
Inpro/Seal has been providing wind energy with permanent bearing protection for over a decade. Check out our resources to learn how we decrease maintenance costs through increased equipment reliability.